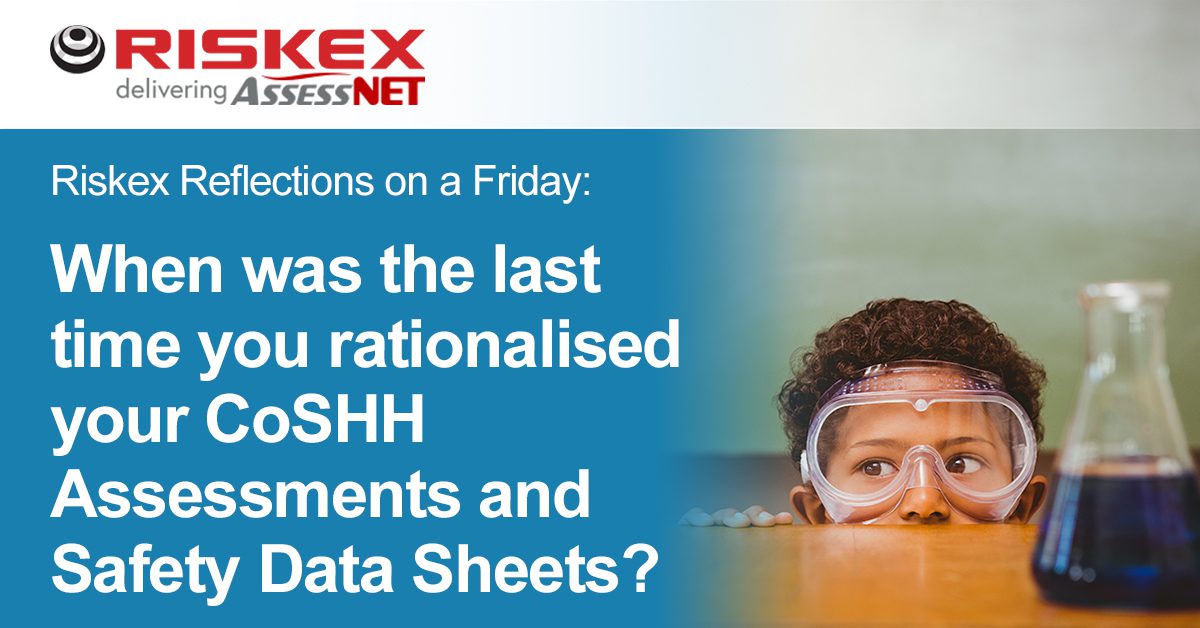
CoSHH Assessments and accompanying SDSs should be revisited to ensure that they are kept up to date and an employer should do this regularly. The date of the first review and the length of time between successive reviews will depend on type of risk, the work, and the employer’s judgement on the likelihood of changes occurring.
When should CoSHH Assessments be reviewed?
Assessments should be reviewed immediately if:
- There is any reason to suppose that the original assessment is no longer valid, eg evidence from the results of examining and testing engineering controls, reports from supervisors about defects in control systems; or
- Any of the circumstances of the work should change significantly and especially one which may have affected employees exposure to a hazardous substance
- The requirement is for a review of the assessment. This does not mean that the whole assessment process will have to be repeated at each review. The first purpose of review is to see if the existing assessment is still suitable and sufficient. If it is, then you do not need to do any more.
- If it appears that the assessment is no longer valid, it does not mean that the whole assessment has to be revised. Only those parts that do not reflect the new situation need amending.
Whether or not there is any real change in the situation, there is an absolute requirement to review the situation on a regular basis. Without this, there is a danger that gradual change over a period of time goes unnoticed and the assessment becomes unsuitable and insufficient by default.
Steps to help you prioritise the most important CoSHH Assessments and their related safety data sheets
- Identify Hazardous Substances: Start by identifying all the hazardous substances used or present in your workplace. This should include chemicals, solvents, gases, dust, or any other materials that may pose health risks.
- Assess the Risks: Evaluate the risks associated with each substance. Consider factors such as toxicity, flammability, reactivity, and potential for exposure. You can use risk assessment tools and guidelines specific to COSHH.
- Consider Exposure Levels: Take into account the likelihood and duration of exposure to each hazardous substance. Substances with a higher likelihood of exposure or those used frequently may require greater attention.
- Review SDS Sheets: Carefully review the SDS sheets for each hazardous substance. Pay close attention to sections that outline the hazards, safe handling procedures, emergency measures, and recommended personal protective equipment (PPE).
- Prioritize Highly Hazardous Substances: Give priority to substances with higher hazard ratings or those that could result in severe health effects, such as carcinogens, mutagens, or substances harmful to the reproductive system. These should be at the top of your list.
- Check Legal Requirements: Review relevant regulations and legal requirements for handling hazardous substances in your region. Prioritise SDS sheets for substances that are subject to specific regulations or have stricter compliance requirements.
- Assess Exposure Routes: Consider how the substances can be absorbed or enter the body (e.g., inhalation, skin contact, ingestion). Prioritise substances with more accessible exposure routes.
- Engage with Employees: Consult with your employees and health and safety representatives to get their input on which substances they believe are most critical to their health and safety. They can provide valuable insights from their daily experiences.
- Historical Incident Data: Analyse historical incident data, such as accidents, near misses, or health-related issues in the workplace. Prioritise substances associated with past incidents.
- Emergency Response: Prioritise SDS sheets for substances that require specific emergency response procedures. Ensure that employees are well-informed about the actions to take in case of accidents or spills involving these substances.
- Training Needs: Consider the training requirements for handling and managing each substance. Prioritise substances that require more extensive training or certification for employees.
- Resource Availability: Assess the availability of resources for implementing control measures. Prioritise substances for which you have the necessary resources for mitigation and monitoring.
- Frequency of Use: Consider how often each substance is used. Frequent use may increase the risk of exposure and should be a factor in your prioritisation.
- Record-Keeping and Documentation: Ensure that you maintain a clear record of your prioritisation process, the reasons for your choices, and any action plans associated with each substance.
By following these steps, you can create a prioritized list of SDS sheets for COSHH, enabling you to focus your efforts and resources on the most critical substances to protect the health and safety of your employees and comply with regulations. Remember that COSHH is an ongoing process, and your prioritisation may evolve as your workplace and chemical inventory change.
Latest News
Riskex Limited
BizSpace
Linford Forum
18 Rockingham Drive
Milton Keynes
Buckinghamshire
MK14 6LY
What3words reference:
Contact us
Make an enquiry:
Company No. 05174302
VAT No. 844 5092 22