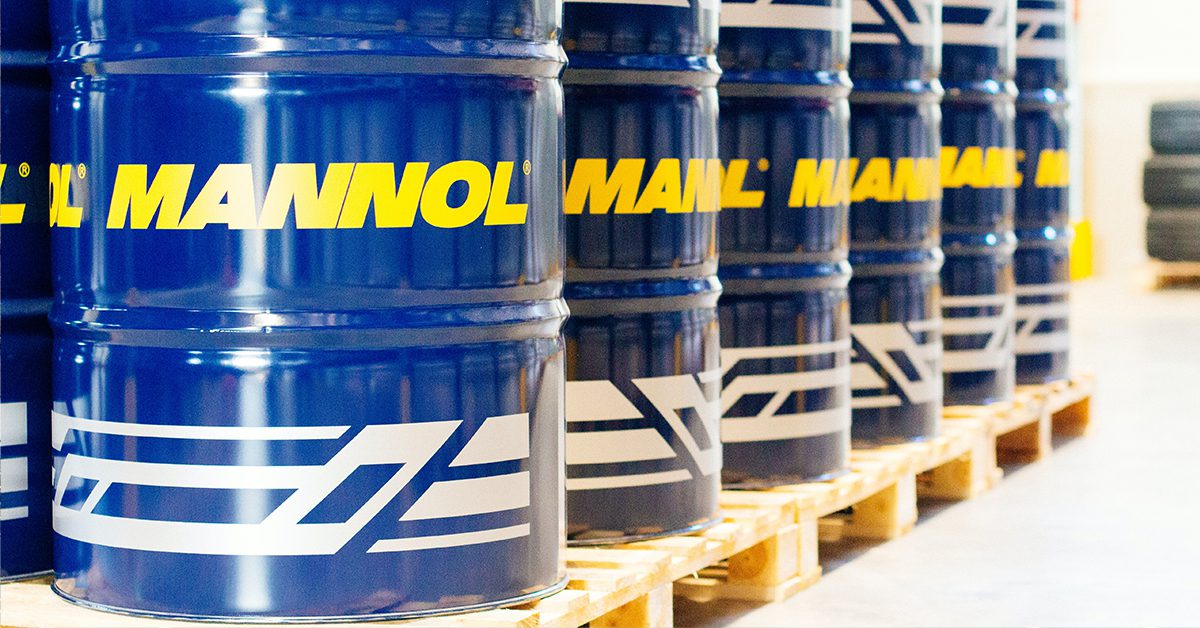
The risks associated with storing hazardous materials vary greatly, depending on the substance itself and the quantity being stored.
When creating COSHH Risk Assessments, the control measures will vary but must consider the properties of the substance to be stored. Different substances create very different risks because of their hazards. Storage conditions will require consideration of the physical and chemical properties, together with the health effects of the substances concerned.
Storing hazardous chemicals is inherently risky. To manage these risks effectively, you will need to fully understand what materials you’re storing, why you’re storing them, where they will be kept, and under what conditions. Aspects to consider:
Keep an up to date SDS library of all materials used within your business: This will allow you to analyse what is in use in your business, helping you to make strategic decisions on usage, alternative products, storage, PPE required, emergency procedures needed and training you need to provide.
Restrict access to chemicals: Ensure access is restricted and only accessible to trained employees. Limiting access to only those who need it will reduce the chance of accidents.
Evaluate what substances are stored together: It is important to know that not all substances are compatible together. Despite being stored in separate containers, in the event of a spillage, leak or other accident these substances could mix resulting in a dangerous combination.
Ensure storage good practice: Make sure there is sufficient space to store all chemicals safely and strategically to avoid accidents. Keep the area well-lit, labelled, signposted and regularly cleaned. Keep the area dry, well ventilated and at a suitable temperature, install an impervious floor that is resistant to the chemicals used and is easy to clean.
Have emergency procedures in place: Be prepared for the worst, evaluate the risks presented by your inventory of materials and prepare for the hazards presented by them. Provide clear up kits, PPE and fire extinguishers in key areas. Regularly reassess and train all employees on these emergency procedures.
Regularly inspect your inventory: Assess the condition of your containers, make sure there are no punctures or leaks. Make sure established protocol is followed and all containers are in the correct location.
Carry out and update COSHH risk assessments: This will help you to better understand the risks involved with specific operations in your business, providing enhanced visibility of your high-risk activities and how the specific chemicals used impact them.
Ensure you have appropriate training plans in place – including refresher training: Training your staff is an essential component of any successful health and safety strategy, regardless of operation or location. In a storage environment, training should include but is not limited to:
- How to safely handle containers to reduce the risk of MSD’s
- Where to obtain PPE and how to use it safely and effectively
- Where to store each COSHH material in use and why
- Where applicable, how to safely operate a forklift
- The emergency procedures you have in place
Specific employee risks: It is important to consider who will be working with specific chemicals and carrying out specific activities and analyse the risk to the individual.
How can AssessNET help?
At Riskex, we specialise in creating cloud-based health and safety software to help businesses optimise EHS performance, remain compliant and improve safety culture. COSHH management is one of our areas of specialism – book a free demonstration of our COSHH / SDS solution today
Latest News
Riskex Limited
BizSpace
Linford Forum
18 Rockingham Drive
Milton Keynes
Buckinghamshire
MK14 6LY
What3words reference:
Contact us
Make an enquiry:
Company No. 05174302
VAT No. 844 5092 22